Ball mill media optimization - Metcom Tech
torque mill test is the mill energy input divided by the solids load. The energy specific cumulative grinding rate at each screen size is calculated from a torque-mill test as in the example that follows. Torque mill solids load during test: 11.25 kg (24.8 lb) of ball mill feed sample from plant survey. Sample is reconstituted with water to be ...
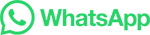