Structuralchangesincalcium silicate hydrate gel and
The obtained C-S-H gel samples were subjected to planetary ball milling at 600 r.p.m. for 1 h using zirconia balls with a diameter of 1 mm. Preliminary experiments performed using acetone and different rotation rates (200, 400 and 600 r.p.m.) had indicated that the structure of C-S-H gel changes dramatically after milling at 600 r.p.m.
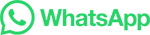