Synthesis and characterization of magnetite-maghemite ...
Mechanosynthesis experiments were performed with a planetary ball mill FRITSCH, model Pulverisette 7 premium line. Two hardened steel vials, 80 cm 3 volume, charged with 60 hardened steel balls 3 mm in nominal diameter, were used as the milling bodies. In both mills, 2.0 g of analytical-grade hematite (α-Fe 2 O 3) with particle size around 0.5 μm, …
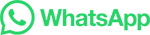