Used Cement Silo for sale. SEMIX equipment & more | Machinio
Used cement silo. Top Seller. SEMIX Cement Silos. Manufacturer: SEMIX. With bolted,welded and horizontal types, silo s are used in storing cement,fly ash,bentonite and other bulk materials.Welded Silo s Welded silo s are preferred in low capacities of storage, it can be assembled and o...
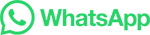