SAG Mill Liners - YouTube
SAG Mill Liners include: feed head & discharge end as well as grates (both outer, middle and inner), pulp lifters (dischargers) shell lifter bars and plates.
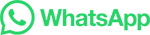
SAG Mill Liners include: feed head & discharge end as well as grates (both outer, middle and inner), pulp lifters (dischargers) shell lifter bars and plates.
The semi-autogenous (SAG) mill grinds materials with steel balls as the grinding media, and is the main grinding equipment in industrial production. Liners are equipped in the internal of the SAG mills, which have the function of protecting the barrel and adjusting the trajectory of the medium.
stresses in large SAG mills helped to drive the development of greatly improved liner materials. However, this cost engineering approach ignored the mill performance and overlooked the other key function of mill liners. The second primary function of a liner is to transfer rotary motion of the mill to the grinding media and charge.
This work characterizes the wear behavior of pearlitic SAG Mill liner material for in-service and laboratory worn samples. The abrasion tests (Dry Sand/Rubber Wheel Abrasion Test – DSRW) were carried out on samples removed from the undeformed region of the same liner – applying different normal loads (from 22 N to 380 N).The electron microscopy …
SAG Mill Liners for Discharge Grate Special Features: The material of SAG mill liner castings are low C or high C Cr-Mo Alloy steel,which depends on the specific working condition of the SAG mill. The hardness of AS2074 L2B is HB310 …
In general, the SAG mill manufacturers will control the addition amount of medium such as steel ball at 2-8%, so that the capacity of semi SAG mill to process materials can be increased by 10-30%. The SAG mill liners wear will increase by 15% due to the impact of medium such as steel ball during the SAG mill operation.
Mill Liner Bolts. Molycop Engineered designs and manufacturers a range of SAG and Ball mill liner bolts for the mining and mineral processing industry. Manufactured from carbon alloy steel, we customize our bolts to satisfy our customer requirements. Molycop Engineered controls the end-to-end process for this product range.
SAG mill liners from Hengin are based on working conditions and mine attributes to carry out structural design, material selection, casting process design, heat treatment process design, manufacturing, on-site tracking and mapping, and continuous optimization and adjustment. Our mining mill liners serve a wide range of users of iron ore, copper ore, molybdenum ore, gold …
The material of SAG mill liners use low or high Carbon Cr-Mo Alloyed steel,the carbon content depends on the working condition of the mill. To choose the right material for the right application is our mission, we are always working together with our customer to achieve this .
High Carbon Chrome Moly Steel SAG Mill Liner (325 to 380BHN) This steel is now considered the main material used for SAG mill liners. There are a number of variations with either different carbon or chrome contents. The variations tend to have a bearing on the size of the liner and its section thickness.
Larger, more competent material consumes mill volume and limits throughput. A number of operations have implemented a secondary crushing circuit prior to the SAG circuit for further comminution of primary crusher product. Such a circuit can counteract the effects of harder ore. coarser ore. decrease the size of SAG mill required, or rectify ...
[8] Royston D. 2007 Semi-autogenous grinding (SAG) mill liner design and development, Miner. Metall. Process 24 121-132. Go to reference in article Google Scholar [9] Powell M. S. and Vermeulen L. A. 1994 The influence of liner …
The two main functions of a mill liner consist in protecting the mill shell against wear and in transmitting the energy of the mill motor to the grinding charge to carry out the required size reduction in the most efficient way. For a mill liner, the design as well as the liner material are to be considered. The required movement of the mill charge to carry out effi-
Force analysis. The main function of the ball mill liner is to protect the mill and use the convex peak of the liner to play the ball to grind and crush the material. Therefore, the main failure mode of the liner is abrasive wear under the repeated impact of small energy. Fig. 1 shows the motion diagram of grinding ball and material.
High Manganese Steel AG Mill Liners Mill Type: AG Mill Hardness: HB310-400 Surface Finish: Ra100 Size Tolerance: as per CT13 Application: AG Mill / SAG Mill Material: Cr Mo Alloy Steel, High Manganese Steel Microstructure: Pearlitical Hardness: HRC32-56 Material Grade: AS20...
Shanghai Bogvik Wear Material Co., Ltd. - Shanghai Bogvik Wear Material Co., Ltd. was originally founded by three young people. ... SAG MILL LINER. Ball Mill & SAG Mill Parts BOGVIK is a trusted supplier of grinding... TOWER MILL LINERS. Ball Mill & SAG Mill Parts BOGVIK is a trusted supplier of grinding... BALL MILL LINER.
As an example at the Kalgoorlie Consolidated Gold 2Mines (WA) 36ft SAG mill the variety of Outer Head Liners was reduced from 36 to 18 items and in doing so decreased the time to replace them by 9 hours at an expense downtime saving of regarding U$ 25,000 per hr. In this instance the liners areas are 3.5 t each.
A metallic liner can be made thinner than other typical liner materials, which is a benefit when a mill is limited by volume. This can improve mill power efficiency and reduce energy wastage, increasing throughput, and operational revenue. 5. Recycled. A worn-out metallic liner can be recycled and sent back to the foundry and used to produce ...
Mill liners fill a basic role: to protect your mills from the intense wear and tear that comes from grinding down hard, raw materials. But even if they all do the same job, not all mill liners are created equal. From the abrasion resistance of rubber to the impact resistance of steel, different material parts offer different advantages. FL supplies the full range of mill liners …
SAG Mill Liner Design In summary: A broad range of AG/SAG circuit configurations are in operation. Very large line plants have been designed, constructed, and operated. The circuits have demonstrated reliability, high overall availabilities, streamlined maintenance shutdowns, and efficient operation.
SAG Mill Liner Design Special Features: The material of SAG Mill Liner Design are low C or high C Cr-Mo Alloy steel,which depends on the specific working condition of the SAG mill.; The hardness of AS2074 L2B is HB310-HB380. We …
A longer lasting mill liner means less downtime for maintenance or new liner installation. A mill liner that occupies less space allows increased volume within the mill and leads to greater grinding capacity and throughput potential. Safer maintenance. 50% lighter and have 50% fewer parts on average when compared to traditional cast steel liners.
Causes Of High Mill Weight In The Sag Mill. Ball mill sag mill ag mill liners.2.Grinding mill liners use case parameters.Hengins cr-mo alloy steel mill liner provides cr-mo lining for citic, tisco, zijin mining, china gold, etc.Cr-mo lining has been widely used in china, australia and other places in copper, gold, iron, molybdenum and other mines.
The mill's continuous operation is interrupted when the mill liner — which comprises riser bar plates that protect the original casing and provide required lift required for grinding action — wears out after months of processing abrasive material. Overall, SAG mills are expensive to operate due to several factors, including high power ...
The biggest characteristic of the sag mill is that the crushing ratio is large. The particle size of the materials to be ground is 300 ~ 400mm, sometimes even larger, and the minimum particle size of the materials to be discharged can reach 0.1 mm. The calculation shows that the crushing ratio can reach 3000 ~ 4000, while the ball mill's ...
These considerations will help determine the best liner material and geometry. Depending on the mill size and material being ground, a lining system can be manufactured from either rubber or composite, with cast metal alloy inserts moulded into the liners at wear critical locations. In large diameter SAG mills, for example, high energy impacts ...
Qiming Casting manufactures AG mill liners, SAG mill liners, and ball mill liners by chrome-moly steel (It is called L2B and L2C grade in Australia standard). This material has excellent wear characteristics with some impact resistance, generally now used for discharge grates where slightly better impact resistance is required compared to the ...
To a more significant degree than in other comminution devices, SAG Mill Liner Design and Configuration can have a substantial effect mill performance. In general terms, lifter spacing and angle, grate open area and aperture size, and …
Nanjing Manganese Manufacturing Co.; Ltd (MGS Casting), which had specialized in casting crusher wear parts, jaw crusher parts, cone crusher parts, impact crusher parts, vsi crusher parts, roll mill parts and other manganese, chrome casting parts over 30 years. Our foundry locates in Gangtang town, Shuangfeng city, Hunan province. Our foundry manufactures more than …
حقوق النشر © 2024.Artom كل الحقوق محفوظة.خريطة الموقع