GrindingExpert™ - WordPress
Our SAG mill strategies automatically adjust feed rate, mill speed and water addition to reduce upsets, eliminate grind-outs, protect liners/lifters, and increase tonnage . We maintain desired operating conditions by constantly monitoring bearing pressure, mill power, recycle pebbles, mill density, charge toe and mill acoustics,
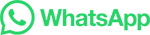