Special Design Solutions - HW Sinto
Sand milling. In order to attain up to 100mm overpressing of the cope part mould, HWS utilises sand milling. This mills the sand with rotating blade heads along the mould flask. The unit can be directly integrated in new moulding systems or retrofitted to existing systems.
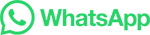