calculation of ball mill design
Ball Mill Design/Power Calculation. 19/06/2015 The basic parameters used in ball mill design (power calculations), rod mill or any tumbling mill sizing are; material to be ground, characteristics, Calculate and Select Ball Mill Ball Size for Optimum Grinding,02/08/2013 Often, the ball used in ball mills is oversize "just in case".
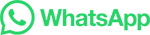