Cement Grinding Aids | Sanghavi Group
Better Particle Size Distribution - Narrower PSD. Increment in Mill Output. Reduction in Specific Power (kWh/ton) of Grinding. Reduction in Mill Run Hours. Improvement in Cement Handling Characteristics. Increment in Cement Flowability & Reduction in Pack-Set.
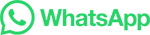