How to Increase Grinding Mill Efficiency?
Well-processed parts will not only increase grinding efficiency, but also offer longer service life. Of cause, the material of roller and ring are all improved. 3. Increase main shaft rotation speed for about 10%, in order to increase the positive pressure when operating. The grinding surface will also increase.
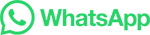