Carbon Dioxide Control Technologies for the Cement …
The cement clinker burning process 3. Assessment of carbon dioxide control technologies 3.1 Pre-combustion technologies 3.2 Oxyfuel technology ... calculations) raw mill raw gas oxygen filter fuel clinker fuel raw material oxygen air air separation nitrogen, inert gases model boundary
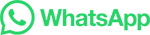