The Effect of Ball Size Diameter on Milling Performance
the mill charge material whereby small diameter balls are used for feed ... size ball mill was used with ball media of sizes 10 mm, 20 mm and 30 mm respectively. Quartz was the material used to perform the experiment and was arranged into 3 mono-sizes namely -8 mm +5.6 mm, -4 mm +2.8 mm and-2 ...
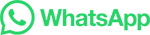