What is CNC Machining and How Does It Work? - 3D Insider
Machining is the process by which raw materials (wood, metal, or plastic among others) are shaped or cut into more useful forms. Manual machining techniques may have been a steadfast element of the Industrial Revolution, but they are now being set aside in favor of computer-aided machining. Nowadays, CNC machining is considered a cornerstone of ...
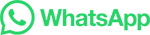