Cement and its effect to the environment: A case study in ...
of other raw materials, grinding of raw materials in the raw mill, storage of raw meal in a raw mill silo, blending of limestone powder to control CaCO3 percentage, burning of raw meal to form clinker, grinding the clinker with gypsum in cement mill and storage of cement in silo packing and distribution of cement.
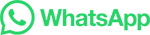