Wet Grinding System Market 2022: Trending Technologies ...
Wet Grinding System market provides a detailed evaluation of the market by highlighting information on different aspects which include drivers, restraints, opportunities, and threats.
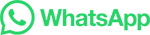
Wet Grinding System market provides a detailed evaluation of the market by highlighting information on different aspects which include drivers, restraints, opportunities, and threats.
Rudnick & Enners wet chip mills are designed for the wet grinding of wood chips or lumpy biomass. The starting material can be ground to a particle size suitable for drying or agglomeration. Depending on the machine configuration and input material, throughput rates of up to 130 loose cubic metres/h are possible (subject to detailed examination of your task).
Wet grinding minimizes specimen heating, and prevents the abrasive surface from becoming loaded with metal removed from the specimen being prepared. Each grinding step, while producing damage itself, must remove the damage from the previous step. The depth of damage decreases with the abrasive size but so does the metal removal rate.
Wet granulation involves the massing of a mix of dry primary powder particles using a granulating fluid.The fluid contains a solvent which can be removed by drying, and should be non-toxic.Typical solvents include water, ethanol and isopropanol and methylene chloride either alone or in combination. The granulation liquid may be used alone or, more usually, as a solvent …
The basket mill is a wet mill that combines dispersion and grinding. It is a continuous batch processing system. The entire grinding process is carried out in the same container. Can achieve ultra-fine grinding. Suitable for mass production, very suitable for different colors, easy to change colors and change products.
Long-Life Grinding Wheels forAngle Grinders— Use on Metals. Wheels are a blend of aluminum oxide and zirconia alumina, which removes more material and lasts three times as long as our General Purpose Grinding Wheels. They are also known as Type 27 wheels, raised-hub wheels, and grinding discs.
Wet grinding The structure of wet ball mill is simple. The discharge port is horn-shaped. There is a screw device in it, which is convenient for discharging materials. 2. Difference in working principle Dry grinding
In this study, to promote the chloride binding capacity of coal fired fly ash (RFA) in cementitious materials, wet grinding was employed and ultrafine fly ash (UFA) with D50 = 2.1 μm was prepared; SEM, XRD, TG, FTIR, and XPS were used to evaluate the chemical and physical change in the process of wet grinding.
Keep in mind that a grinding wheel is a form of cutting tool, and except in the case of wheel for general purpose grinding, the abrasive, grit size, grade and structure, bond type should be selected to fit the particular job on which the wheel is to be used, just as a cutter, drill or tap is selected for its specific job.
In season, grind when drastic changes in snow are expected (dry to wet and vice versa). Early Spring, prepare the skis for late season wet snow conditions. Base Structure . General Advice. Don't belt grind race skis. Belt grinding is not the same as stone grinding. A belt grind will not produce a flat base.
As my previous article of Grinding Machine, I told, grinding is an important operation in manufacturing industry to get a final product, so for that, we need to know about the grinding wheel and its properties so that we easily choose a right wheel for the right material.. I assumed that you already have a brief idea about Grinding Machine. Don't worry! if you not learned yet …
Dry and wet grinding are two common and effective grinding methods. Usually, in the machine used for dry grinding, the material will contact and hit other particles or rotors in a closed area until it is broken into the required size. Dry milling can make particles reach micron size. But if you want to achieve smaller nanometer sizes, wet ...
Core Technology Of Wet Grinding . High Value Equipment Productivity Solutions Allwin Patented Technologies - High pressure resistant mechanical seal structure, patent No.: ZL 2016 2 0406106.6 - Grinding system cooling structure, patent No.: ZL 2016 2 0406502.9 - Detachable grinding cylinder, patent No.: ZL 2016 2 0398691.X
Mixer Mill MM 500 control. The MM 500 control is a high energy laboratory ball mill that can be used for dry, wet and cryogenic grinding with a frequency of up to 30 Hz. It is the first mixer mill in the market that allows to monitor and control the temperature of a grinding process. The temperature area covers a range from – 100 to 100 °C.
In addition, with wet grinding there is little breakage of the mineral structure, in contrast to dry grinding [5]. Therefore, from the viewpoint of decreasing the grain size of materials, wet ...
The Choice of the right grinding wheel depends on Material to be ground and its hardness. Amount of stock removal and finish required. Wet or dry grinding. Wheel speed. Area of grinding contact. Severity of grinding operation. Condition of machine. The Three components of a grinding wheel are The ABRASIVE grains that do the actual … CHOICE OF GRINDING …
5.Vijay Associates – Wet Grinder Manufacturers. Established in the year 2000, Vijay Associates in Avarampalayam, Coimbatore is a top player in the category Wet Grinder Manufacturers in the Coimbatore. This well-known establishment acts as a one-stop destination servicing customers both local and from other parts of South India. Over the ...
Therefore, the wet grinding method came into being, and the powder obtained by wet grinding is the most effective and economical method. It avoids the high cost of chemical nano-powder manufacturing, and also avoids the shortage of mechanical dry grinding fineness that is difficult to reach nano-level powder. Generally, the particle size of dry ...
Grinding Wheel in Industry. A vitrico grinding wheels is the most common equipment in the metallurgy industry. Grinding Wheel cuts metals with different sizes, shapes, and efficiency. Grinding Wheel is generally composed of two types of materials
The best wet grinding wheels on the market are based on a sophisticated system and are made by Tormek in Sweden. The initial purchase price, however, may well exceed some budgets. On the other hand, with a good whetstone, a grinding guide and a certain amount of practice, your results will be perfectly adequate.
Fine grinding produces a surface with little deformation that can easily be removed during polishing. Because of the drawbacks with grinding papers, alternative fine grinding composite surfaces are available, in order to improve and facilitate fine grinding, A high material removal rate is obtained by using grain sizes of 15, 9.0 and 6.0 µm.
UNIT 2 GRINDING Grinding Structure 2.1 Introduction Objectives 2.2 Types of Grinding 2.3 Shapes and Size of a Grinding Wheel 2.3.1 Straight Wheel ... classified as dry grinding and wet grinding. When cutting fluid is spread over the workpiece, wheel face and sides, it is named as wet grinding. The commonly used
detailed comparison between Dry-grinding Iron Ore Tail ings (DIOTs) and Wet-grinding Iron Ore Tailings (WIOTs) was made. This comparison was based on particle characterist ics, crystal structures, chemical structure, and surface properties. The results showed that the particle size of IOTs reduced rapidly during wet grinding. In addition, WIOTs
Wet Pan Grinding is also called Wet Grinding Machine. Based on the different structure it is divided into double roller grinding and three roller grinding. They are mainly used for grinding operation, such as all kinds of ferrous metal, non-ferrous metal, non-metallic minerals, and the separation of gold, silver, lead, iron, copper and so on..
Abstract. In this paper, the effect of wet grinding on structural properties of ball clay is undertaken. The wet grinding treatment was performed employing ball and vibro mills for different time spells of 2, 4, 8 and 16 hours. The structural properties were carried out using X-ray diffraction (XRD).
Wet Pan Mill is also called Wet Grinding Machine. Based on the different structure it is divided into double roller grinding and three roller grinding. Wet pan mill mainly used for grinding operation, such as all kinds of ferrous metal, non-ferrous metal, non-metallic minerals, and the separation of gold, silver, lead, iron, copper-gold and so on.
The compact structure makes the butter maker machine popular both for home and commercial use to grind roasted nuts, peanut, cashew nuts, cocoa mass and chocolate coating, etc. Buy it with + + Total price: To see our price, add these items to your cart. ... Premier Small Wonder Table Top Wet Grinder 1.5 Liter,110 volts by SS Premier.
Through wet-grinding process, WGKL with D50 of 0.64 μm was prepared, and more amorphous structure and higher ion dissolution were observed. (2) WGKL increased the 16 h compressive strength of PC and greatly shortened the setting time. 4% WGKL increased the 16 h
wet grinding until 500 kJ/kg specific grinding work the median particle size decreased significantly, however higher specific grinding works did not resulted in lower median size, at 6 and 10 m/s as well. With the applied grinding parameters lower median size than 840-900 nm could not reached by wet grinding.
These grinders are used for grinding round and hollow jobs whether the internal surface of this job is completely round, ditched round, or is in taper. Small grinding wheels of 3 cm to 5 cm, are used in such grinders. Sometimes grinding wheels of special shape 0.2 cm to 0.3 cm. These grinders can be divided into two parts. a. Chucking Grinder
حقوق النشر © 2024.Artom كل الحقوق محفوظة.خريطة الموقع