Pellet mill design - Feed Strategy
Chapter 3: Pellet Mill Design fluctuate due to the variation in feed ingredients and formulations, as well as to the pellet quality desired. The pellet mill manufacturer should be consulted as necessary for the ideal set-up regarding other applications or applications with non-typical ingredients. Table 3 -1.
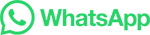