Bar Rolling Production Process - Steel Rolling Mill Machine
Bar Rolling Production Process. News / By Hani Tech. Products. Bar & Wire Rod Rolling Mill (10) News (94) Rebar Rolling Mill (9) Short Stress Path Rolling Mill (2) Spare Parts (2) Uncategorized (1)
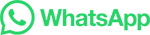