The Hot Rolling Process - California Steel
The Hot Rolling Process The primary function of the Hot Strip Mill is to reheat semi-finished steel slabs of steel nearly to their melting point, then roll them thinner and longer through 12 successive rolling mill stands driven by motors totaling 77,000 hp, and finally coiling up the lengthened steel sheet for transport to the next process.
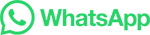