In-Process Monitoring and Analysis of Bearing Outer …
stages, such as roughing, semi-finishing, finishing and spark-out, as shown in Fig. 2. To simulate the multi-infeed grinding behaviour, the real infeed rate r& in different stages must be known. Fig. 2 Typical power curve of internal plunge grinding For internal plunge grinding, n is used to represent the order of the infeed stage,
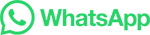