Cement Ball Mill - JXSC Machine
The cement ball mill is mainly used for grinding the finished products and raw materials of cement plants, and is also suitable for grinding various ore and other grindable materials in industrial and mining enterprises such as metallurgy, chemical industry, and electric power. Cement grinding is the last process of cement production, it is to ...
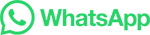