Strength of Concrete: Nature, Kinds and Factors | Concrete ...
1. Type of Cement: Type of cement influences the strength development in concrete to a great extent depending upon its chemical composition and fineness of grinding. The percentage of C 3 S in concrete is responsible for the higher strength development upto 28 days, while C 2 S contributes to strength development after 28 days.
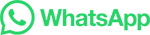