20150505 Bond Efficiency-GMG-ICE-v1-r04 Determining the ...
use a rod mill F80 of 16,000 µm and a rod mill P80 of 1,000 µm. Note that—in order for no correction factor for ball mill product fineness to apply—the ball mill circuit P80 should be no less than approximately 70 µm (Bond, 1962). This Bond …
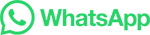