The effect on the Performance of Cement Grinding Aid ...
According to the 95% clinker + 5% gypsum cement mixing ratio, when the grinding clinker (1-7 mm), gypsum and grinding agent to join together Φ 500 x 500 national cement plant in the unified test standard laboratory mill grinding together, each timegrinding 5 kg, grinding time for 40 min, the release time for 5 min. 2.2.2 Performance Test
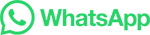