Resminer- Ball Mill Liner Supplier in China
WHY Choose Resminer Ball Mill Liner Supplier. If you need a high quality of mill liners that has longer life service, Resminer mill liner is the perfect solution. We are more than 30 years in providing high quality of wear resistance materials such as grinding balls, cylpebs, mill liner, toggle plate, liner plate, crusher parts, Etc.
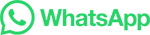