Gearless mill drives - ABB
• 28 MW GMD for a 40' SAG mill • 28 MW GMD for 42' SAG mill Whether it is size or an installation at the highest altitude (4600 m.a.s.l.), ABB's GMDs are well positioned to contribute to the building of larger and ever more powerful mills. — Leading the gearless mill drive evolution The ABB gearless mill drive (GMD) is the most powerful ...
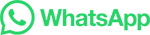